Inverted Bucket Steam Trap Armstrong
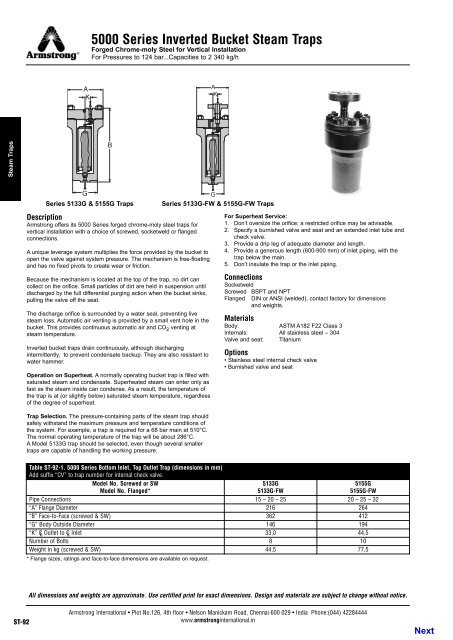
A unique leverage system multiplies the force.
Inverted bucket steam trap armstrong. Gradual wear slightly increases the diameter of the seat and alters the shape and diameter of the valve. Armstrong has been sharing know how since we invented the energy efficient inverted bucket steam trap in 1911. An armstrong inverted bucket steam trap continues to operate efficiently with use. Armstrong 814 816 series inverted bucket steam traps cast iron pressures to 250 psig 17 bar capacities to 20 000 lb hr 9072 kg hr.
Capacities to 4 400 lb hr 2 000 kg hr the most reliable steam trap known the inverted bucket provides efficient condensate drainage of virtually all types of steam using equipment. Armstrong s developments and improvements in steam trap design and function have led to countless savings in energy. Cast iron for horizontal installation. Capacities to 4 400 lb hr 2 000 kg hr armstrong offers two sizes of cast steel inverted bucket traps with in line horizontal pipe connections and integral strainers with a choice of screwed socketweld or flanged connections.
How to use the inverted bucket trap capacity chart to select an inverted bucket steam trap using the armstrong capacity chart you must know the condensate load safety factor and pressure differential remember the objective is always to select a trap that can 1 operate at the maximum differential pressure and 2 handle the capacity at the. In the years since customers savings have proven again and again that knowledge not shared is energy wasted. Armstrong 2000 series inverted bucket steam traps all stainless steel with universal connector pressures to 650 psig 45 bar capacities to 1 300 lb hr 590 kg hr. But as this occurs a tight seal is still preserved the ball merely seats itself more deeply.
For pressures to 250 psig 17 barg. Cast steel for horizontal installation with integral strainer for pressures to 600 psig 41 barg. This operating efficiency means less fuel is burned in turn reducing emissions and saving money.